切削工具は、製造業や金属加工業において欠かせない存在です。しかし、工具の寿命が短くなると、生産効率が低下し、コストの増大を招くことがあります。
特に、工具の摩耗や破損が予期せず起こると、現場のオペレーターや技術者にとって大きなストレスとなり、計画外のダウンタイムが発生することもあります。
そこで本記事では、切削工具の寿命を判別する方法から、寿命を延ばすための具体的なポイントまでを詳しく解説します。現在、工具の寿命に悩んでいる方や、より効率的な工具運用を目指す方にとって役立つ情報を提供しますので、ぜひ最後までご覧ください。
また、以下の記事ではクーラント濾過装置導入でおすすめのメーカーを紹介していますので、気になる方はぜひ参考にしてみて下さい。
切削工具の種類と特性について
切削工具には多くの種類があり、それぞれが特定の加工目的に最適化されています。主な種類とその特性について理解することは、適切な工具選定と寿命延長の第一歩となります。
エンドミル
エンドミルは、側面と先端の両方に切れ刃を持つ円筒形の工具です。平面加工、側面加工、溝加工、3D形状の加工など、多目的に使用されます。材質としては、高速度鋼(HSS)、粉末ハイス、超硬合金、サーメット、CBN、ダイヤモンドなどがあり、加工対象や要求精度によって選択します。
特に超硬エンドミルは、耐摩耗性と耐熱性に優れており、高速加工や硬質材料の加工に適しています。ただし、衝撃に弱いという特性があるため、断続切削には注意が必要です。最近では、ナノコーティング技術の進歩により、TiAlN、TiCN、DLCなどの表面処理が施された高性能エンドミルも増えています。これらのコーティングは工具表面の硬度と潤滑性を向上させ、結果として工具寿命を大幅に延ばす効果があります。
ドリル
ドリルは穴あけ加工に使用され、ツイストドリル、ガンドリル、センタードリルなど様々な種類があります。材質選択とともに、ポイント角、ヘリックス角、先端形状などの幾何学的特性も重要なパラメータです。
最新のドリル技術では、内部クーラント通路を持つタイプが増えており、これにより切削点へ直接クーラントを供給することができ、加工熱の効率的な除去と切り屑の排出を促進します。特に深穴加工では、この内部クーラント機能が工具寿命を大幅に延ばす鍵となります。
旋削工具(バイト、インサート)
旋削工具は、旋盤加工で使用される工具で、単一の切れ刃を持ちます。ソリッドタイプとインサートタイプがあり、現代の製造現場では交換式インサートが主流となっています。
インサートは、形状、サイズ、材質、コーティングなど多様なバリエーションがあり、ISO規格によって標準化されています。適切なインサート選択は、加工精度、表面品質、工具寿命に直接影響します。例えば、正のすくい角を持つインサートは切れ味が良く低い切削抵抗を示しますが、耐久性では負のすくい角を持つインサートに劣ります。
フライス
フライスは、主に平面加工や段差加工に使用される回転工具です。フェイスミル、ショルダーミル、ボールエンドミルなど、加工形状によって多様なタイプがあります。
マルチインサート式のフライスカッターでは、各インサートの位置調整(ランニングアキュラシー)が重要で、これが不適切だと特定のインサートに負荷が集中し、工具寿命が著しく短くなる可能性があります。また、断続切削によるショックを軽減するためのダンピング機構を備えた高性能フライスも開発されています。
これらの切削工具は、それぞれ特有の摩耗パターンや寿命特性を持っています。工具の種類と特性を深く理解することで、適切な使用方法と管理が可能となり、結果として工具寿命の延長につながります。
切削工具の寿命は?判別する方法
切削工具の寿命は、決まった数値で判断できるものではなく、使用環境や頻度に大きく左右されます。しかし、寿命が近づいていることを示すいくつかの兆候があります。
以下のポイントに注意することで、工具の交換タイミングを把握しやすくなります。
- スラッジが細かくちぎれている
- 切削の精度低下
- 異音や振動の増加
- 表面粗さの変化
- 消費電力の上昇
- 加工時間の延長
切削作業中に発生するスラッジ(削りかす)が、通常より細かくちぎれている場合、切削工具の刃先が摩耗し始めている可能性があります。特に、切れ味が低下して材料を削り取る力が弱くなった場合は、寿命が近いと判断できます。
寸法精度が安定しない、または仕上がりが粗くなるといった場合も寿命のサインです。これは、工具の摩耗が進んだ結果であり、加工面が求められる品質基準に達しなくなることを意味します。
切削中に異音や異常な振動が発生する場合は、刃先や工具本体が劣化している可能性があります。これらの判別方法を把握しておくことで、予期せぬトラブルを防ぎ、切削工具の交換タイミングを適切に判断する助けとなります。
寿命を超えた工具を使用することのリスク
切削工具を寿命以上に使い続けると、生産効率や品質、コスト、安全性において大きなリスクが生じます。また、摩耗が進むと加工精度が悪化し、製品品質が低下して再加工や廃棄のリスクが高まります。
さらに、破損リスクも増大し、作業員の安全を脅かし、工作物や機械にもダメージを与える可能性があるため、注意が必要です。これらのリスクを避けるためには、工具の寿命を見極め、定期的なメンテナンスと適切な交換を行うことが必要不可欠です。
品質リスク
工具寿命を超えて使用すると、加工精度の悪化が加速度的に進行します。例えば、微細加工において、工具摩耗が0.1mm増加すると、製品の寸法誤差が最大0.3mm拡大する可能性があります(材料や切削条件によります)。これにより、部品の組み立て精度や機能性に直接影響を及ぼし、最終製品の性能低下や不良につながります。
特に航空宇宙や医療機器など高精度が要求される分野では、わずかな寸法誤差も許容されません。実際のケーススタディでは、工具寿命を超えた使用により、高精度部品の不良率が正常時の3〜5倍に上昇した事例が報告されています。
経済的リスク
工具寿命を超えた使用は、短期的なコスト削減に見えて、実際には総コストの増加を招きます。例えば、10,000円の工具を交換せずに使い続けた結果、以下のような追加コストが発生する可能性があります。
- 再加工コスト: 不良品を修正するための追加工数(人件費、機械稼働費)
- 材料廃棄コスト: 修正不可能な場合の材料損失
- 納期遅延によるペナルティ: 顧客との契約違反による罰金や信用損失
- 機械修理コスト: 工具破損による機械損傷の修理費
ある製造企業の分析によれば、工具寿命を20%超過して使用した場合、工具コスト自体は節約できても、全体のプロセスコストは平均で40%増加したというデータがあります。
安全リスク
工具の突然の破損は、作業者の安全に直接関わる重大な問題です。高速回転する工具が破損すると、破片が高速で飛散し、目の損傷や顔面外傷などの人身事故を引き起こす可能性があります。
また、工具破損による機械の急停止は、キャリッジやテーブルの衝突につながり、CNC機械の軸やベアリングに深刻なダメージを与えることがあります。こうした損傷の修理には、数十万円から数百万円のコストがかかる場合があります。
安全管理の観点からは、工具寿命管理を徹底することで、年間の作業関連事故を最大60%削減できたという製造現場の事例もあります。これは間接的なコスト削減(労災保険料の低減、労働損失時間の減少など)にもつながります。
切削工具の寿命が短くなる原因
寿命を超えた工具は、作業効率の低下や製品品質の不安定化を引き起こし、最終的にはコスト増加につながる可能性があります。以下に、切削工具の寿命が短くなる具体的な原因をまとめました。
それぞれを詳しく解説していきます。切削工具の寿命が短くなる主な原因には、使用頻度の高い作業や過剰な切削負荷などが挙げられます。
特に高硬度の材料を加工する場合、工具にかかる負担が大きくなり、摩耗や破損が早まります。適切な使用環境や条件を維持しないと、工具の寿命を大幅に短縮するリスクが高まります。
摩耗による工具損傷
摩耗した工具を使用し続けることで、加工精度が悪化し、製品の仕上がりにばらつきが出ることがあります。
また、摩耗した工具は、通常の作業よりも高い切削抵抗を必要とするため、機械にかかる負荷も増加し、結果的に設備にも悪影響を及ぼす可能性があります。
工具摩耗には、フランク摩耗、クレータ摩耗、ノッチ摩耗、チッピングなど様々な形態があります。これらは発生メカニズムが異なり、対策も違います。
- フランク摩耗(逃げ面摩耗): 最も一般的な摩耗形態で、工具の逃げ面が徐々に削られていきます。主な原因は、工具と加工材との摩擦による機械的摩耗です。硬質コーティングの採用や、適切な切削速度の選定で軽減できます。
- クレータ摩耗: 工具のすくい面に火山の噴火口のような凹みができる摩耗です。高温による拡散摩耗が主因で、耐熱性の高い工具材質やコーティングの採用、十分なクーラント供給で対策できます。
- ノッチ摩耗: 切れ刃と加工面の境界部分に生じる局所的な摩耗です。加工硬化した表面層や酸化被膜との接触が原因で、切り込み量の調整や工具の定期的な位置変更で軽減できます。
工具摩耗は完全に避けることはできませんが、適切な対策により進行速度を遅らせることが可能です。例えば、TiAlNコーティングを施した超硬工具は、無コーティング工具と比較して最大3倍の寿命延長が期待できるという研究結果があります。
破損による工具損傷
切削条件が不適切であると、工具が過度な負荷を受けて破損することがあります。例えば、切削速度や角度の設定が間違っていると、工具に急激なストレスがかかり、刃先が欠けたり折れたりする原因となります。
破損は一瞬で起こるため、加工作業が停止し、工具交換によるダウンタイムが発生するリスクが高まります。
工具破損の主な原因と対策は以下の通りです。
- 熱衝撃: 急激な温度変化による破損です。断続切削時や、クーラント供給が不均一な場合に発生しやすくなります。対策としては、予熱切削(最初は低速で切削を始め、徐々に速度を上げる方法)や、クーラント供給の最適化が効果的です。
- 過負荷: 工具の強度を超える切削力が加わると、瞬時に破損します。特に薄刃工具や小径工具で顕著です。切削深さと送り速度の適切な設定、トロコイダル加工などの高度な加工戦略の採用が効果的です。
- 疲労破壊: 長時間の使用による微小亀裂の蓄積が原因です。定期的な工具検査と、推奨使用時間を守ることが重要です。予防的な工具交換戦略を導入することで、突発的な破損を防止できます。
- 不適切なランニングイン: 新しい工具を使い始める際、最初から高負荷をかけると破損リスクが高まります。新工具は最初の数分間、通常の70-80%程度の切削条件で使用し、刃先を馴染ませることが推奨されます。
工具破損を防ぐためには、加工シミュレーションソフトウェアの活用も効果的です。最新のCAM(Computer Aided Manufacturing)システムでは、切削力や工具たわみをシミュレーションし、破損リスクを事前に評価することができます。これにより、実際の加工前に潜在的な問題を特定し、加工パラメータを最適化することが可能になります。
メンテナンス不足による損傷
定期的なメンテナンスやクリーニングを怠ると、切削工具の性能が劣化しやすくなります。切削くずの除去や工具のクリーニングを適切に行わないと、工具に不要な負荷がかかり、摩耗や損傷の原因になりやすいです。
また、クーラント液の管理が不十分な場合も工具の冷却や潤滑が不十分となり、寿命が短くなります。
効果的な工具メンテナンスには以下の要素が含まれます。
- 定期的なクリーニング: 切削加工後、工具に付着した切粉や油分、加工材の残留物を適切に除去することが重要です。特に、超音波洗浄機やスペシャルクリーナーを用いた定期的な洗浄は、微細な切れ刃の保護に効果的です。
- 適切な保管: 工具は湿気や腐食から保護するため、防湿キャビネットや専用ケースに保管することが推奨されます。特に、高価な超硬工具やCBN工具は、適切な保管がさらに重要です。中小企業でも導入可能な温湿度管理された工具保管システムは、工具寿命を15-20%延長する効果があるという報告もあります。
- 定期的な検査: 光学顕微鏡やデジタルマイクロスコープを用いた定期的な工具検査は、微小な損傷を早期に発見するのに役立ちます。現代の製造現場では、画像認識技術を活用した自動検査システムも普及しつつあります。
- 適切な再研削: HSS工具などの再研削可能な工具は、専門の研削サービスや適切な工具研削機を用いて定期的に再研削することで、繰り返し使用が可能です。ただし、再研削の回数や方法が不適切だと、かえって工具性能を損なう可能性があるため注意が必要です。
実際の製造現場での調査によれば、体系的な工具メンテナンスプログラムを導入することで、年間の工具コストを平均20-30%削減できたという事例も報告されています。これは直接的な工具購入コストの削減だけでなく、工具交換頻度の低減による生産性向上にも貢献します。
切削工具の寿命を延ばすための3つのポイント
切削工具の寿命を延ばすためには、適切な切削条件の設定、定期的なメンテナンスとクリーニング、そしてクーラント液の寿命を延ばすことが重要です。
これらのポイントを取り入れることで、工具の摩耗や損傷を抑え、交換頻度を減らすことができます。
それぞれのポイントを詳しく見ていきましょう。
適切な切削条件の選定
切削条件を正しく設定することで、工具にかかる負荷を減らし、寿命を延ばすことが可能です。特に切削速度や送り速度、切り込み深さの設定は、工具の摩耗に大きく影響を与えます。
加工材の種類や硬度に応じた適切な切削条件を選定し、無理のない加工を行うことで、工具の摩耗や破損リスクを軽減できます。
定期的なメンテナンスとクリーニング
工具の寿命を延ばすためには、定期的なメンテナンスが欠かせません。切削作業後に工具のクリーニングを行い、切削くずや汚れを除去することで、工具の表面が滑らかに保たれ、摩耗の進行を防げます。
また、使用頻度に応じて工具の点検や研磨を行うことで、工具の状態を良好に保ち、寿命を延ばすことが可能です。
クーラント液の寿命を延ばす
切削工具の寿命において、クーラント液の管理も重要です。工具の冷却と潤滑に役立ち、摩耗や焼き付きのリスクを抑える効果があるものがクーラント液です。
クーラント液を定期的に交換し、清潔な状態を保つことで、工具にかかる熱や摩擦を効果的に抑え、結果的に工具の寿命を延ばすことができます。
また、クーラントろ過システムを導入することで、クーラント液の品質を維持し、長期的なコスト削減も期待できます。これらのポイントを実践することで、切削工具の寿命を延ばし、コストを削減しつつ作業効率を高めましょう。
精密クーラントろ過システムなら濾過精工株式会社がおすすめ
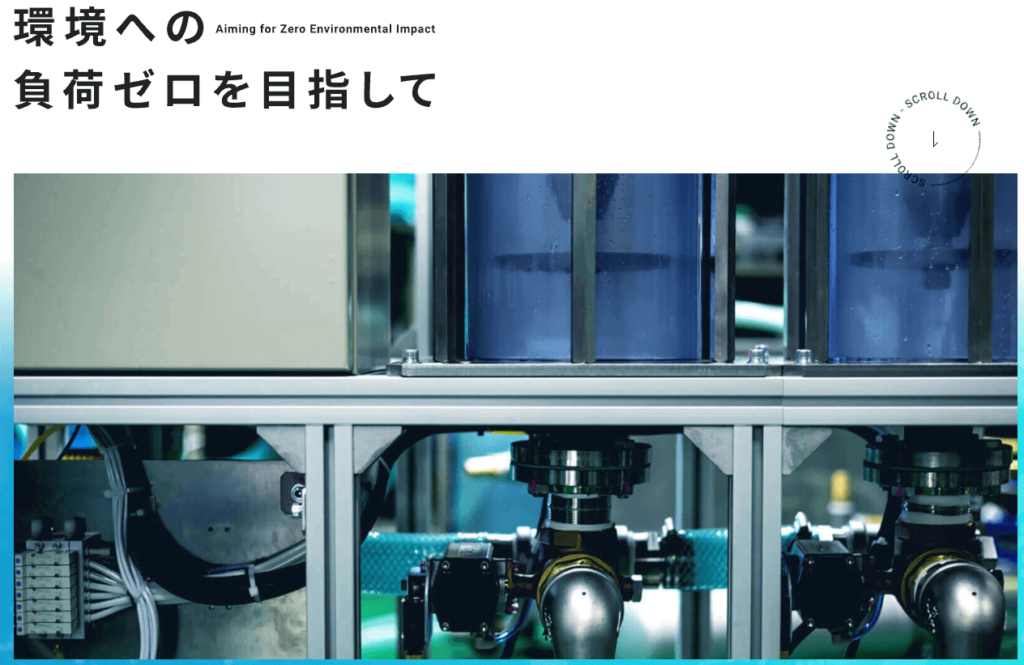
項目 | 詳細 |
---|---|
会社名 | 濾過精工株式会社 |
設立年月日 | 2011年9月 |
資本金 | 6,470万円 |
所在地 | 東京都中央区日本橋蛎殻町 1-10-1 ゲーテハウス株式会社内5階 |
電話番号 | 03-6264-8575 |
公式HP | https://www.rokaseiko.com/ |
切削工具の寿命を延ばすためには、適切な切削条件の選定や定期的なメンテナンス、さらにクーラント液の品質管理が重要です。クーラント液の管理は、工具の冷却・潤滑効果を維持するため、摩耗や焼き付きのリスクを抑えるためにも欠かせません。
ここで、精密なろ過が求められるクーラント液を使用する切削作業におすすめしたいのが、濾過精工株式会社の精密クーラントろ過システムです。
濾過精工株式会社の製品は、1μm未満の微細なスラッジまで確実に除去できる高いろ過能力を持っており、クーラント液の清浄度を極限まで高めることが可能です。
工具への不要な負荷が軽減し、結果として寿命が延び、交換頻度の低減やコスト削減が期待できます。
工具の性能を最大限に引き出し、長期的な運用コストの抑制を目指す企業には、濾過精工株式会社のクーラントろ過システムの導入を検討されることをおすすめします。
以下の記事では濾過精工の会社の特徴や商品などを詳しく解説していますので、気になる方はぜひ一度お読みになってみてください。
まとめ
切削工具の寿命を延ばすためには、適切な切削条件の選定、定期的なメンテナンス、クーラント液の品質管理が重要です。
工具の寿命が短くなる原因には、摩耗や破損、メンテナンス不足があり、これらを放置すると、生産効率の低下や品質の悪化、コストの増加といったリスクが伴います。
しかし、ポイントを押さえた管理を行うことで、工具の交換頻度を減らし、コスト削減と作業効率の向上を図ることが可能です。日々の業務の中で、工具の状態を意識し、必要なメンテナンスを行うことが工具の寿命延長に繋がります。
これらの対策を積極的に取り入れ、現場の生産性向上に役立ててください。